Industrial Heater Rentals Fort McMurray
Providing safe, breathable heat while maintaining ambient conditions.
Tank coating is a sensitive operation which requires a high degree of precision. Ambient conditions must be consistently maintained to make coatings last longer and avoid rework. The right industrial heater must be selected to maintain a consistent ambient temperature.
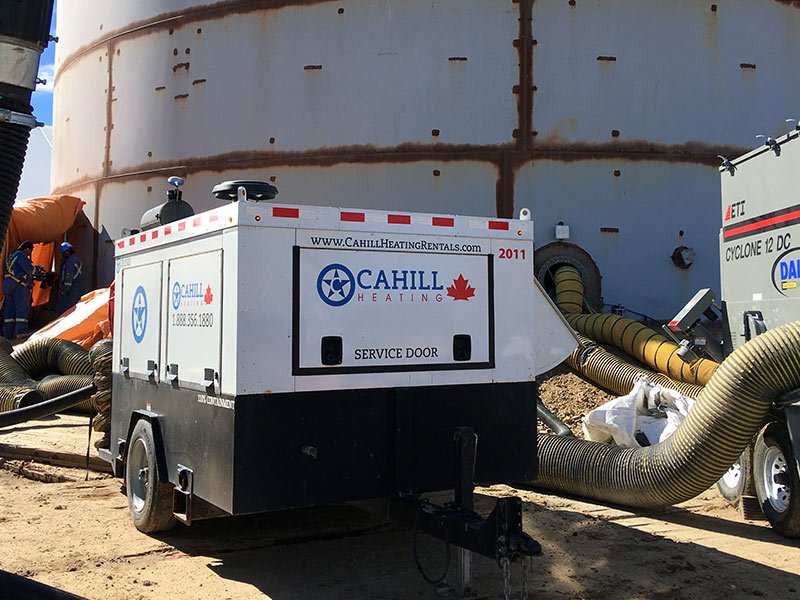
A leading coatings contractor undertook a tank coating contract at a major refinery in Alberta, Canada. With constantly fluctuating weather, maintaining an ambient temperature was a major challenge. The contractor observed that the commercial heater on site did not deliver heat evenly, leading to the thickening and sagging of the coating. Also, the air delivered from the heater drove the humidity up, leading to longer coating times.
With each passing day, the threat of missing deadlines and having to rework loomed largely. At this point, the contractor decided to replace the heaters on site with Cahill’s patented CH15MS heaters. Featuring an inbuilt thermostat, Cahill’s portable heaters allow the customer to adjust the temperature to maintain an ideal ambient temperature.
The hot, dry air delivered through portable ducting helped control the humidity to speed up the coating process.
With safety features that guarantee zero leakage and are designed to deliver perfectly breathable air, the heaters keep the workers safe and warm throughout the operation. Featuring a 14″ static pressure, the Cahill heaters could deliver hot air from hundreds of feet away.
The technology switch allowed the customer to eliminate the threat of rework and helped them complete the tank coating job several days in advance. This allowed for early tank commissioning and had a direct positive impact on revenue.