Managing Moisture in Temporary Worksites: Climate Control Best Practices
Temporary worksites—such as construction sites, industrial projects, and remote job sites—face unique environmental challenges, with moisture buildup being one of the most persistent and problematic issues. Excess moisture can cause structural damage, equipment failure, and unsafe working conditions. Implementing effective climate control strategies is essential to maintaining a dry, efficient, and safe workspace.
This article explores the impact of moisture on temporary worksites, why moisture control is critical, and the best industrial climate control solutions for effective moisture management—even in remote locations.
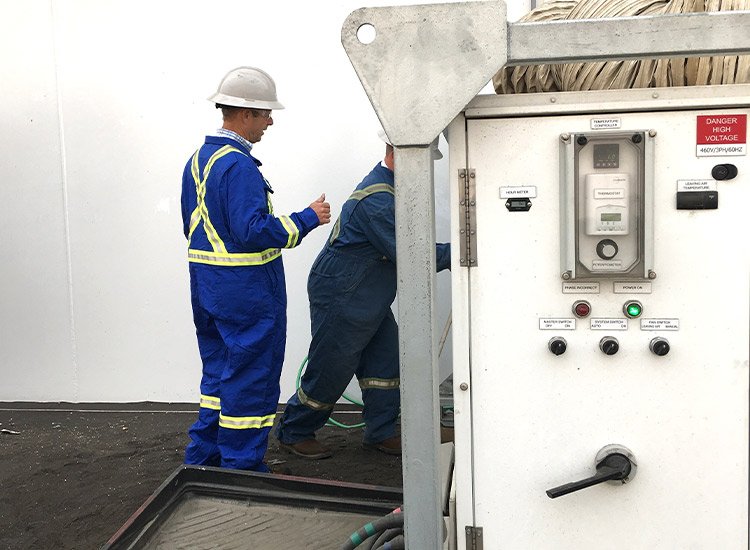
The Impact of Moisture on Temporary Worksites
Moisture is a silent yet hazardous issue in many temporary worksites. Whether caused by weather conditions, high humidity, or poor ventilation, excessive moisture can lead to several challenges, including:
- Mold and Mildew Growth
- Rust and Corrosion
- Structural Damage
- Equipment Malfunctions
Seasonal and Environmental Factors Contributing to Moisture Buildup
Temporary worksites are particularly vulnerable to seasonal changes. In winter, condensation forms when warm indoor air meets cold surfaces. This temperature difference can create damp conditions inside enclosed structures without proper climate control.
Warmer seasons also present moisture-related challenges. High summer humidity can cause materials to absorb moisture, increasing the risk of mold growth and warping. Additionally, outdoor and semi-covered worksites must be prepared for rain and flooding, which can quickly introduce significant amounts of water into the work area.
Compliance with Safety and Industry Regulations
Moisture control is not just about protecting materials and equipment—it is also a legal requirement in many industries. Occupational health and safety regulations mandate proper climate control to protect workers and prevent hazards such as mold exposure, electrical malfunctions, and structural instability. Adhering to best practices for moisture management helps companies stay compliant, avoid costly fines, and prevent project delays.
Climate Control Solutions for Moisture Management
Effective climate control is essential for preventing moisture-related damage. The following solutions help keep temporary worksites dry and safe:
Dehumidification Systems: Industrial dehumidifiers are crucial in controlling moisture levels by removing excess humidity from the air. These systems help:
- Prevent mold and mildew growth
- Protect materials from moisture absorption
- Maintain a comfortable and safe work environment
Heating Solutions: In colder climates, indirect and flameless heaters regulate temperatures and reduce condensation by:
- Preventing moisture buildup on surfaces
- Keeping materials dry and preventing freezing
- Maintaining a stable work environment during winter months
Cooling Systems: During hot and humid conditions, air conditioning and HVAC systems help manage humidity by:
- Reducing excess moisture in the air
- Creating a comfortable work environment for employees
- Preventing equipment overheating and condensation
Best Practices for Effective Moisture Management
Renting innovative industrial equipment and implementing the right climate control strategies is only part of the solution. To ensure long-term moisture control at your worksite, follow these best practices:
1. Conduct a Moisture Assessment Before Setup
Before establishing a temporary worksite, perform a moisture assessment to identify potential problem areas. Consider factors such as location, exposure to weather conditions, seasonal humidity levels, and the risk of water intrusion from rain, groundwater, or condensation.
2. Choose the right Climate Control Equipment
Selecting the appropriate climate control equipment is essential for maintaining optimal conditions. When determining what you need, consider the size of the enclosed area, expected humidity levels, and seasonal temperature variations.
3. Monitor Humidity Levels with Sensors and Data Loggers
Regular monitoring ensures that climate control systems are functioning effectively. Site managers can use hygrometers to measure relative humidity and set up automated alerts for sudden changes in moisture levels.
4. Properly Store Moisture-Sensitive Materials
Materials such as wood, drywall, and electronics require proper storage to prevent damage. To keep them safe:
- Store materials off the ground on pallets whenever possible.
- Use moisture-resistant covers or tarps.
- Keep sensitive materials in climate-controlled enclosures when available.
- Maintain and Inspect Climate Control Systems Regularly
5. Maintain and Inspect Climate Control Systems Regularly
Routine maintenance ensures that dehumidifiers, heaters, and ventilation systems operate efficiently. Best practices include:
- Cleaning filters and air ducts regularly.
- Checking for leaks or blockages.
- Testing equipment before extreme weather conditions occur.
Moisture Management for Temporary Worksites
Managing moisture in temporary worksites effectively is essential for maintaining safe, efficient, and compliant operations. By understanding the challenges moisture presents and implementing the right climate control solutions, businesses can prevent costly damage, protect worker health, and ensure project success.
A proactive approach to moisture management not only preserves equipment and materials but also fosters a safer and more productive work environment. Investing in proper climate control strategies today can save time, money, and potential setbacks in the future. Contact Cahill Heating Rentals today to find the best climate control solutions for your next project.